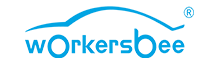
What Are You Looking For?
Electric vehicles (EVs) are reshaping the future of transportation, and their widespread adoption depends on reliable charging infrastructure. At the heart of this infrastructure are EV charging connectors, which must endure diverse environmental conditions while maintaining optimal performance. One critical aspect of ensuring their durability is corrosion resistance, which prevents rust and degradation over time. At Workersbee, salt spray testing plays a vital role in delivering high-quality, rust-resistant charging connectors that meet the demands of the EV industry.
In this article, we explore the importance of corrosion resistance in EV charging connectors, the role of salt spray testing in enhancing product durability, and how Workersbee’s rigorous testing protocols reinforce our commitment to quality.
What Is Salt Spray Testing?
Salt spray testing, also known as salt fog testing, is a laboratory-based method used to simulate corrosive environments and evaluate the resistance of materials to rust and degradation. It involves exposing products to a saline mist in a controlled chamber, mimicking conditions they may encounter in real-world environments such as coastal regions or areas with heavy industrial pollution.
At Workersbee, we adhere to industry standards like ISO 9227 to ensure our testing processes deliver consistent and reliable results. This enables us to assess the durability of our EV charging connectors and optimize them for long-term use.
The salt spray testing process involves placing charging connectors inside a specialized chamber where a fine mist of saline solution is continuously sprayed. The chamber is maintained at a controlled temperature and humidity, replicating years of exposure to harsh conditions in a matter of days.
This accelerated testing allows us to identify potential vulnerabilities, such as surface pitting or material breakdown, that could compromise the performance and safety of our products. By simulating real-world challenges, salt spray testing ensures our connectors are ready to withstand the elements.
Why Corrosion Resistance Matters for EV Charging Connectors Preventing Rust and Electrical Failures
Rust and corrosion are not just aesthetic issues—they can have serious implications for the functionality and safety of EV charging connectors. Corrosion can increase electrical resistance, leading to overheating, inefficiency, and even failure of the connector. In severe cases, it could pose a safety risk to users.
Salt spray testing helps us identify and eliminate these risks by ensuring our connectors resist the corrosive effects of moisture, salt, and other environmental factors. This rigorous testing guarantees that our connectors maintain their electrical conductivity and mechanical integrity over time.
Extending Product Lifespan
Durability is essential for EV charging connectors, especially those installed outdoors where they face constant exposure to the elements. Corrosion can significantly reduce the lifespan of connectors, leading to frequent replacements and higher maintenance costs.
Through salt spray testing, we ensure our connectors are built to last. By using corrosion-resistant materials and protective coatings, we deliver products that offer long-term reliability, reducing downtime and enhancing customer satisfaction.
Workersbee’s Approach to Salt Spray Testing
At Workersbee, we utilize state-of-the-art salt spray chambers to conduct comprehensive corrosion resistance evaluations. These chambers are designed to replicate a wide range of environmental conditions, including neutral salt spray (NSS) and cyclic corrosion tests, which simulate alternating wet and dry conditions for a more realistic assessment.
Our equipment meets stringent international standards, including ISO, IEC, and SAE protocols, ensuring that every test is accurate and reliable. By investing in cutting-edge technology, we demonstrate our commitment to producing durable and dependable EV charging connectors.
Strict Testing Protocols
Our salt spray testing process follows a meticulous protocol to ensure consistency and precision. Each test is conducted under controlled conditions, with parameters such as temperature, humidity, and saline concentration carefully monitored.
Before a product is approved for production, it must pass a series of rigorous tests to identify and address any potential weaknesses. This thorough approach allows us to deliver connectors that meet the highest standards of quality and performance.
Material Selection and Coating Optimization
Salt spray testing provides invaluable insights into the performance of different materials and coatings. By evaluating their resistance to corrosion, we can make informed decisions about the components we use in our connectors.
For example, stainless steel and nickel-plated contacts are preferred for their exceptional resistance to rust and environmental degradation. Protective coatings are also optimized to provide maximum durability without compromising the connector’s electrical performance.
Improving Product Resilience in Harsh Environments
EV charging connectors are often deployed in challenging environments, from coastal areas with salty air to urban locations exposed to industrial pollutants. Salt spray testing allows us to simulate these conditions and ensure our products can perform reliably in any setting.
This resilience is particularly important for public charging stations, where connectors must withstand heavy use and harsh weather conditions. By rigorously testing our products, we ensure they can meet the demands of any application.
Workersbee’s Commitment to Product Quality
At Workersbee, quality is the foundation of everything we do. Salt spray testing is a testament to our dedication to delivering reliable and long-lasting EV charging solutions. By demonstrating the durability of our products through rigorous testing, we build trust with our customers and reinforce our reputation as a leader in the industry.
Delivering Rust-Resistant Connectors for a Sustainable Future
As the world transitions to cleaner transportation, the demand for dependable EV charging infrastructure continues to grow. Workersbee is committed to meeting this demand by producing connectors that combine durability, safety, and performance. Salt spray testing plays a critical role in achieving this mission, ensuring our products are ready to support the future of electric mobility.
Conclusion
Salt spray testing is more than a quality assurance method—it’s a reflection of Workersbee’s commitment to excellence. By simulating real-world corrosive environments, this testing process allows us to deliver EV charging connectors that are built to last. From material selection to advanced testing protocols, every step of our process is designed to ensure the highest levels of durability and reliability.
As we continue to innovate and set new benchmarks in the EV industry, our focus remains on delivering products that exceed customer expectations. At Workersbee, we don’t just test for quality—we engineer it into every connector we produce.
Discover Workersbee’s Industry-Leading EV Charging Solutions
Explore our range of corrosion-resistant EV charging connectors and experience the difference that rigorous quality assurance makes. Contact us today to learn more!