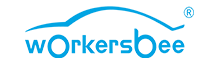
What Are You Looking For?
In the previous articles, we have fully understood the important role of liquid cooling technology in DC fast charging and become familiar with some key components. Before the liquid-cooled charging cables are truly put into use in Electric vehicle infrastructure, strict and comprehensive testing is critical, as these tests are closely related to the safety and reliability of liquid-cooled charging.
In this article, we will briefly introduce some key tests for liquid-cooled charging plugs/cables to help you face high-power EV charging solutions with more confidence. The following tests may be involved to ensure that the liquid-cooled charging equipment maintains stable performance and safety during high-power transmission and long-term operation.
1. Sealing Test
This primarily includes Air Tightness Testing, Leakage Testing, and High-temperature Operation Testing, which are particularly important for Eco-friendly EV charging.
Air tightness testing aims to detect the sealing performance of the liquid-cooled tubes and connectors and can be used as an equivalent test method to IP67. Compared to the IP67 submersion test, the air tightness test can be conducted without causing damage. Whether the air tightness meets the standard can be judged by the leakage rate.
Leakage testing is a type test used to verify the long-term sealing performance of various components and the compatibility of the coolant. The high-temperature operation test is conducted to verify whether the sealing components remain effective at high temperatures.
2. Temperature Rise Test
The Temperature Rise Test is a fundamental test for liquid-cooled charging equipment. In the power-on state, the temperature difference between the charging plug, cable, and other components and the ambient temperature is the temperature rise at each test point. This is an important indicator when using High-power chargers.
The liquid-cooled plug test requires the collection of the temperature, flow rate, and pressure values of the inlet and outlet liquid cooling tubes. This includes tests when the liquid cooling system is turned on and off, meaning it has two rated current values. The temperature rise under each current is converted into a derating curve of the charging plug to determine the allowable rated current at different ambient temperatures.
Additionally, a Short-term Failure Test of the Liquid Cooling System is necessary to simulate the safety performance of the liquid cooling plug when the system suddenly fails. It is required that after the test, there is no damage or leakage in the cable, liquid cooling tube, and other components of the charging plug.
The temperature rise test is an important gatekeeper for achieving Efficient energy management.
3. Liquid Cooled Tube Strength Test
As a key component of the liquid-cooled cable, the liquid-cooled tube may not only be frequently bent but also bear the pressure of the coolant.
Therefore, it is common to measure the structural strength of the cable through a Bending Test to detect any bulges or breaks in the cable after repeated bending. This ensures that the continuity of the conduct wires and the air tightness of the plug and liquid-cooled tube meet the standard requirements.
The Burst Pressure Test of the liquid-cooled tube is conducted to evaluate the pressure resistance of the liquid-cooled pipe under high-pressure conditions, ensuring that it does not rupture or leak during actual use, thus guaranteeing the safety and reliability of the charging process.
4. Mechanical Performance Test
This may include the Plug Insertion and Extraction Test (insertion and extraction force, insertion and extraction life, etc.), Impact Resistance Test (side strength test, vibration resistance test, etc.), and Cable Tensile Test (tensile strength, etc.). These tests are used to evaluate the reliability of the charging plug in daily use, ensuring that the mechanical structure is sturdy and durable, and capable of adapting to various harsh operating environments.
5. Durability Test
In actual use, charging plugs may undergo multiple insertions and extractions, high temperatures, low temperatures, or other harsh conditions. Therefore, it is necessary to test their performance under these conditions to evaluate their service life and reliability.
For example, by simulating the wear of long-term use, the lifespan and aging of the charging plug can be detected to ensure that it has sufficient durability.
Additionally, salt spray tests and internal corrosion tests can assess the charging plug’s resistance to harsh environments such as moisture and salt corrosion.
6. Compatibility Test
Charging plugs need to have broad compatibility to adapt to different vehicle models’ charging inlets and communication protocol requirements.
It is necessary to ensure that the charging connector can properly connect to the charger and the electric vehicle and establish communication according to the predetermined charging protocol to initiate charging, guaranteeing widespread applicability in practical use.
7. Electrical Safety Test
This includes insulation performance testing, leakage protection testing, overtemperature protection testing, current-voltage load testing, overcurrent, and overvoltage protection testing, as well as tests for protection against water, dust, and moisture.
It ensures that the liquid-cooled charging cables can supply power stably under various operating conditions and will not cause dangerous incidents in possible abnormal or extreme situations, thus safeguarding the safety of users and vehicles.
8. User-Friendliness Test
This involves simulating the actual usage scenarios of drivers to assess the comfort of the charging process from the user’s perspective. It includes noise testing, insertion, and extraction force testing, as well as the weight, size, flexibility, and ease of operation of the charging connector. The goal is to ensure a barrier-free and pleasant experience for users during the charging process.
Satisfactory Workersbee CCS2 Liquid Cooled DC Cable Temperature Rise Test Performance
As a global leading charging plug solution provider, Workersbee’s product development has always been at the forefront of Sustainable charging technology.
Our CCS2 liquid-cooled charging plug 2.0 can deliver a stable continuous current output of 500A, with peak output reaching up to 700A. Testing engineers connected the sample to the liquid cooling system and series-connected it to a DC voltage-stabilized power source, testing the current at 500A, 600A, and 700A until the temperature stabilized. A temperature acquisition instrument was used to detect the cable (head, middle, tail), plug breech DC+, plug breech DC-, temperature sensor DC+, and temperature sensor DC-. The following data was obtained:
1. Test current at 500A, the highest temperature rise after stabilization was at the plug breech DC-: 31K.
2. Test current at 600A, after 34 minutes of testing, the highest temperature rise was at the plug breech DC-: 50.7K.
3. Test current at 700A, after 7 minutes of testing, the highest temperature rise was at the plug breech DC-: 48K.
Choose Workersbee Liquid Cooled Charging Cables for Your Business
· Rigorous and comprehensive product testing system
· Outstanding charging performance and liquid cooling capabilities
· Multiple international authoritative certifications
· Customized charging solutions based on your business needs
· Complete after-sales service system
Conclusion
In addition to routine tests such as the critical sealing test and the basic temperature rise test, the charging plug must undergo many other professional tests related to hardware, software, and user experience before being incorporated into charging facilities.
By conducting comprehensive and meticulous professional tests on the EV liquid-cooled charging plug, it is ensured that it maintains stable performance and reliability in high-power and high-current transmission and during prolonged operation.
Workersbee is committed to research and development innovation and always adheres to high production quality standards. We look forward to working with you to connect our liquid-cooled charging cables, which have undergone rigorous testing, to your advanced charging network. We aim to provide electric vehicles with a safe, fast, and convenient charging experience, to empower sustainable transportation, and to add vitality to our beloved planet.